Table of Contents
-
1. Traditional Scanners, a.k.a. “Expensive Hardware That Breaks When You Need It Most”
-
2. The "Scan and Pray" Approach Isn’t Sustainable
-
3. Traditional Barcodes Don’t Hold Up to Real-World Conditions
-
4. Manual Maintenance Nightmares
-
5. Scaling Limitations: The "One-Size-Fits-None" Problem
-
Next-Level Inventory Management Tips
-
The Modern Barcoding Solution for Modern Event Businesses
Inventory management can make or break your business. Traditional barcoding systems have long been considered a “necessary evil” in the events industry — especially for AV companies, production houses, and rental businesses managing high-volume inventory. But what if your barcoding system is actually holding you back?
Today, we’ll explore five critical limitations of conventional barcoding solutions and how Goodshuffle Pro’s innovative approach transforms inventory management for modern event businesses.
1. Traditional Scanners, a.k.a. “Expensive Hardware That Breaks When You Need It Most”
If you’ve worked with traditional barcoding systems, you know the frustration all too well. Those clunky $700+ scanners always seem to fail at the worst possible moments — like during a late-night load-out when you’re racing against the clock.
Not only is the setup cost for traditional scanners ridiculously expensive (the $3,000-$4,000 set up price tag is often unattainable for many smaller companies), but rental businesses find themselves constantly replacing these expensive devices, creating a recurring cost that adds up quickly. And when a scanner breaks mid-event? Your entire inventory process grinds to a halt.
The Next-Level Solution: Goodshuffle Pro’s Barcoding feature eliminates the need for dedicated scanning hardware altogether. Your team can use the smartphones they already carry to scan inventory items with industrial-grade precision. This mobile-first approach means no more investment in costly equipment that breaks down or needs replacement — just lightning-fast scanning so intuitive your team can get trained in minutes.
2. The "Scan and Pray" Approach Isn’t Sustainable
Traditional barcoding gives you basic confirmation that an item was scanned, but little else. When items don’t get scanned back in after an event, you’re left playing detective:
- Which crew member handled it last?
- What event did it come from?
- Is it damaged, lost, or just misplaced?
This limited visibility creates accountability gaps and makes it nearly impossible to trace what actually happened to your missing gear.
The Next-Level Solution: Goodshuffle Pro’s Barcoding system creates timestamped Activity Logs that document exactly who handled each item and when. This creates clear accountability and eliminates the dreaded “Who had that last?” finger-pointing when equipment goes missing. Plus, items can be instantly marked with status updates (damaged, cleaning needed, etc.) during check-in, so you’ll always know why something isn’t ready for the next job.
3. Traditional Barcodes Don’t Hold Up to Real-World Conditions
Standard barcode systems work fine in perfectly controlled environments, but event rental businesses rarely operate in perfect conditions. Try scanning items in a dimly lit warehouse corner, or capture a worn label that’s been exposed to the elements after a rainy outdoor wedding. Traditional scanners struggle with:
- Low-light conditions in venues or warehouses
- Damaged or partially torn labels
- Scanning from odd angles when items are stacked
- Tiny barcodes on small inventory items like cables
The Next-Level Solution: Goodshuffle Pro’s advanced scanning technology works in virtually any condition. The industrial-grade scanning capability can capture barcodes from a distance, even at odd angles, in low light, or with damaged labels. This means your crew can keep scanning efficiently even in the most challenging environments, at a remarkable rate of up to 480 scans per minute.
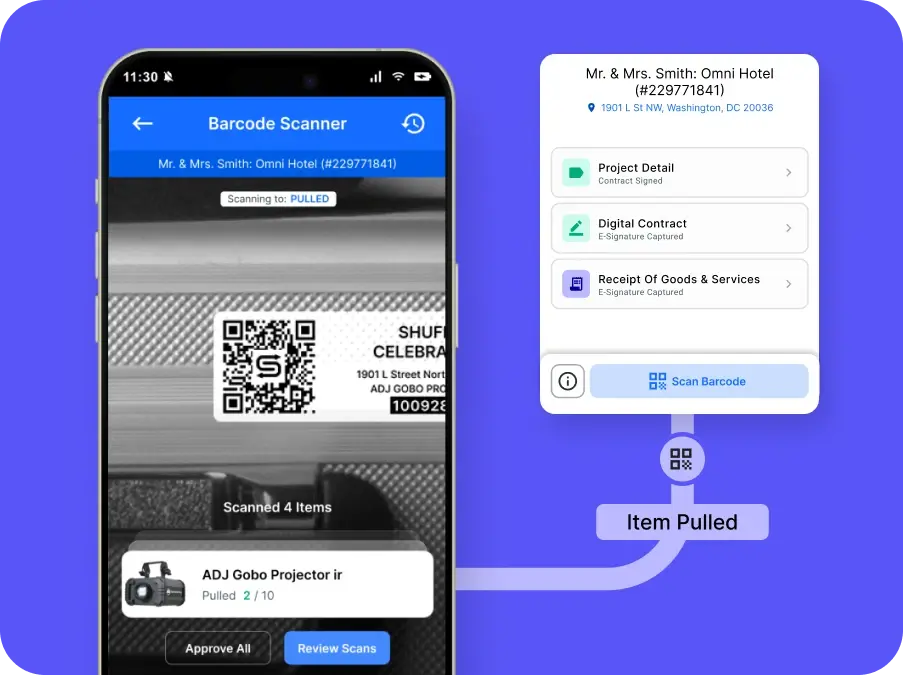
4. Manual Maintenance Nightmares
The ongoing maintenance of traditional barcoding systems is a hidden cost that drains resources:
- Constantly reprinting labels that fall off or become unreadable
- Managing separate barcode generation software
- Training new staff on complex scanning protocols
- Dealing with system compatibility issues
Many event businesses report spending hours each week just maintaining their barcoding infrastructure instead of focusing on growth.
The Next-Level Solution: Goodshuffle Pro automates barcode generation within the platform itself, allowing you to print directly from your standard printer or a recommended LabelWriter for more durable tags. This eliminates the need for third-party barcode generation tools and simplifies your entire workflow. The system is so intuitive that new crew members can learn it in minutes, reducing training time and operational headaches.
5. Scaling Limitations: The "One-Size-Fits-None" Problem
Perhaps the biggest limitation of traditional barcoding is how poorly it scales with your business. Many systems charge per inventory item, making it cost-prohibitive to track every cable, connector, or small accessory. This forces companies to make uncomfortable choices about which items “deserve” tracking and which don’t.
Additionally, conventional systems often can’t handle high-volume scanning efficiently. When you need to process hundreds of chairs after a wedding or dozens of speakers after a concert, scanning each item individually creates massive bottlenecks.
The Next-Level Solution: Goodshuffle Pro’s Barcoding was built specifically for volume and scale. The bulk scanning capability lets you process multiple items simultaneously — perfect for managing hundreds of cables, chairs, or lighting fixtures. And since there’s no per-item cost, you can barcode everything from your most expensive console to your smallest adapter without worrying about costs ballooning as your inventory grows.
Next-Level Inventory Management Tips
Ready to do away with inventory management headaches? Here are key strategies to implement when upgrading your barcoding approach:
- Start with high-value and commonly lost items: Focus your initial barcoding efforts on expensive equipment and items that frequently go missing.
- Create a standardized labeling system: Establish consistent placement of barcodes on similar items to speed up the scanning process.
- Use Barcoding to identify items: Random cable lying on the warehouse floor and not sure what project(s) it belongs to? You can quickly scan it to pull up item details and see all the projects it’s on.
- Implement batch scanning procedures: Train your team to scan groups of similar items together for maximum efficiency during busy load-ins and load-outs.
- Use the Activity Log proactively: Review who handled what after each event to identify patterns and improve accountability.
- Integrate Barcoding with maintenance processes: Use check-ins and check-outs as an opportunity to mark items as Set Aside and add internal notes, so repairs can happen more quickly.
The Modern Barcoding Solution for Modern Event Businesses
Traditional barcoding systems were designed for retail and industrial environments — not the unique challenges of the events industry. Goodshuffle Pro’s Barcoding feature was built from the ground up for event professionals who need to process inventory quickly in unpredictable conditions.
By eliminating expensive hardware, improving visibility, working in any environment, minimizing maintenance, and scaling effortlessly, next-generation barcoding transforms what was once a “necessary evil” into a genuine competitive advantage.
Your inventory is one of your most valuable assets. Isn’t it time you managed it with tools designed specifically for your business?
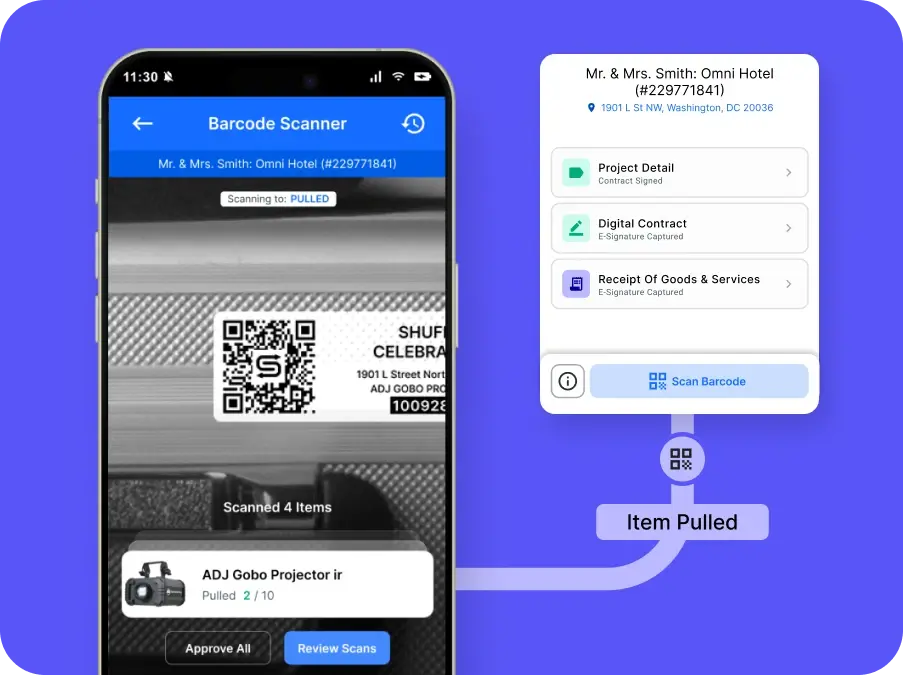